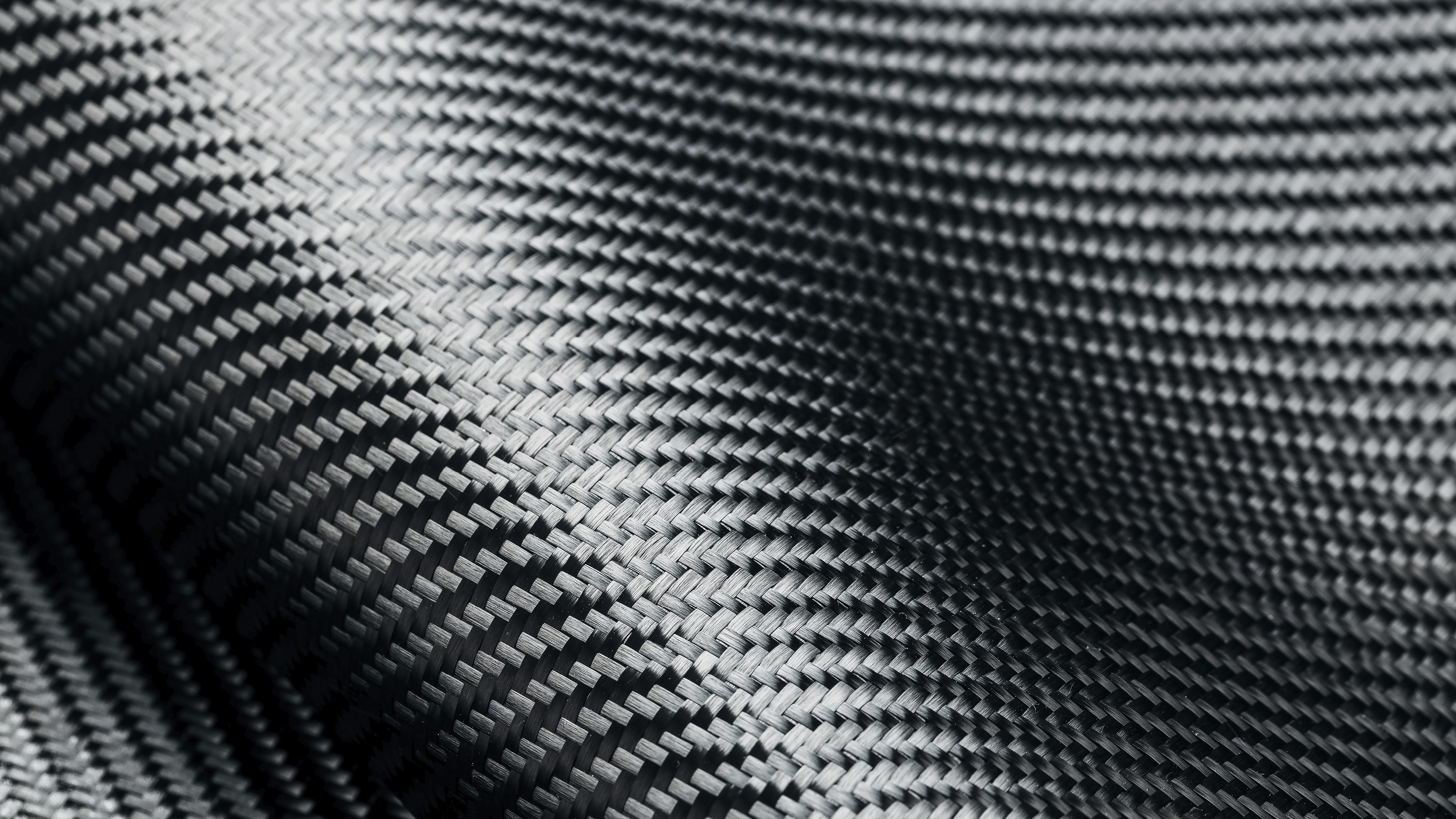
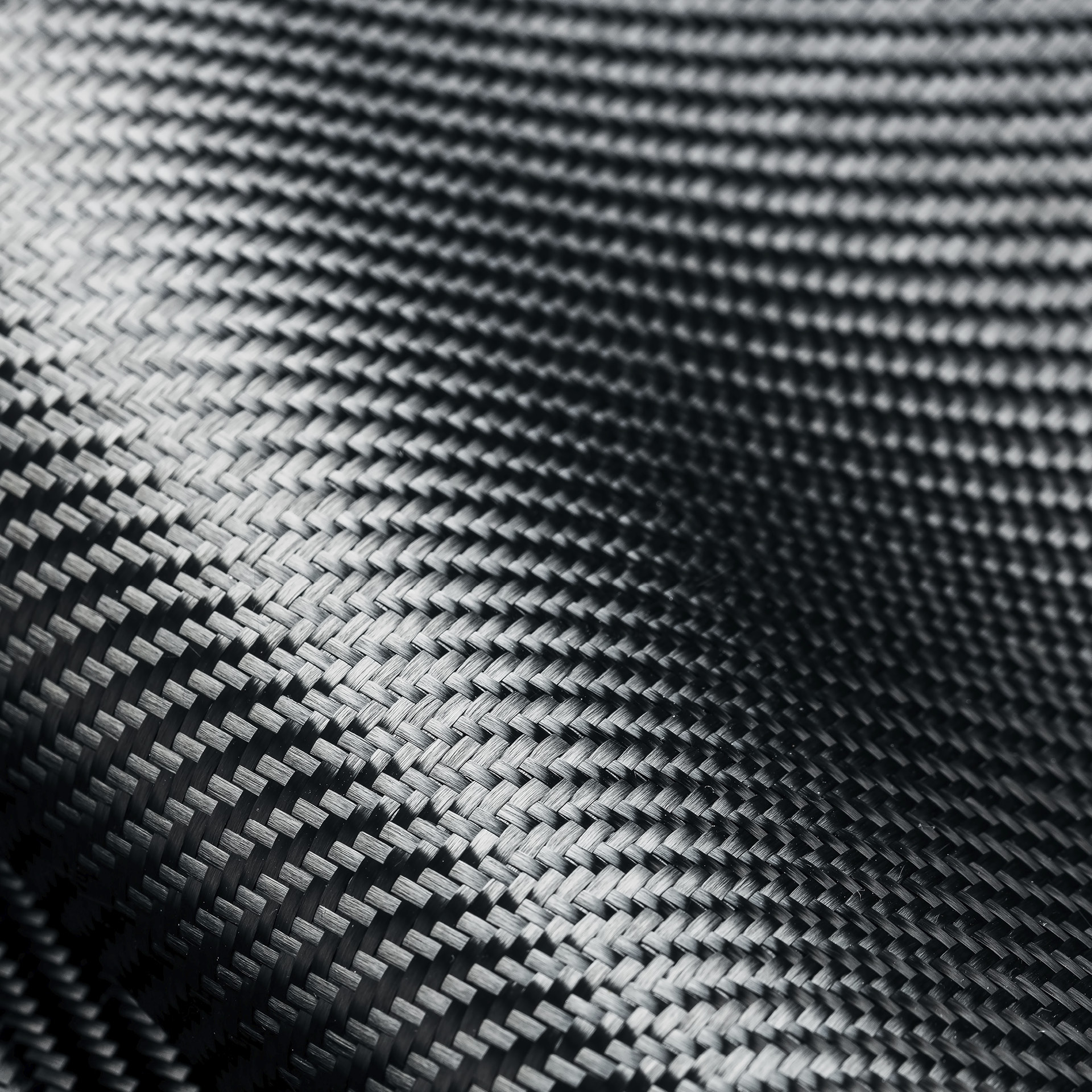
2025.02.20 현대자동차그룹
미래에는 지금보다 더 뛰어난 성능과 효율성을 지닌 모빌리티가 요구된다. 현대자동차그룹을 포함한 많은 모빌리티 기업이 복합소재(Composite Material) 연구개발에 매진하는 이유다. 복합소재란 두 개 이상의 물질을 결합해 각 물질이 단독으로 존재할 때보다 더 좋은 물성을 띠게 되는 소재를 의미한다. 재료의 혼합 비중이나 적층 방식에 따라 원하는 물성을 다양하게 얻을 수 있어 널리 쓰인다. 대표적인 예가 ‘탄소섬유강화플라스틱(CFRP)’이다. 가볍고 튼튼해 산업은 물론 일상 제품에도 널리 사용된다.
복합소재는 주성분인 모재(Matrix)와 물성을 보강하는 강화재(Reinforced Material)로 구성된다. 모재는 강화재를 접착하고 보호하는 역할을 하고 주로 수지(Resin), 금속, 세라믹 등을 사용한다. 강화재는 강성, 강도 등의 특성을 강화하는 역할을 하며 섬유(Fiber), 구상입자(Particle), 편상입자(Flake) 등의 다양한 형태가 있다.
복합소재의 장점은 서로 다른 재료의 이점을 극대화하는 것이다. 예컨대 강화재로 주로 쓰이는 탄소섬유(Carbon Fiber)는 지름이 5~15μm에 불과할 정도로 가늘지만 인장강도와 강성도가 높다. 이를 이용해 원하는 모양의 직물을 짜고 모재인 합성수지를 혼합 후 열을 가해 탄소섬유강화플라스틱을 만든다. 탄소섬유로 인장강도와 강성을, 합성수지로 내충격성을 확보하는 것이다. 덕분에 탄소섬유강화플라스틱은 금속보다 가벼우면서도 잘 휘어지지 않으며 외부 충격에 강하다.
조합에 따라 원하는 물성을 얻을 수 있다는 점에서 복합소재는 자동차, UAM, 로봇 등 미래 모빌리티의 필수 적용 소재로 여겨지고 있다. 다양한 물성을 활용해 효율성을 높이고 품질을 개선할 수 있기 때문이다. 그렇다면 현재 복합소재는 어떻게 활용되고 있을까? 현대차그룹의 사례를 통해 알아봤다.
차체는 자동차에서 가장 무거운 부위다. 따라서 많은 자동차 제조사가 차체의 무게를 줄이려 다양한 방법을 시도하고 있다. 현대차·기아는 복합소재 기술로 차체의 무게를 줄이고 있다. 초저비중 실러(초경량 접착제)가 좋은 예다. 실러는 차체 패널이 겹치는 부위를 밀봉하고, 금속에 녹이 발생하는 것을 방지하는 접착제다. 보통 차량 1대당 170m 정도의 실러가 쓰이며, 총 무게는 약 8kg다.
현대차·기아가 사용하는 초저비중 실러는 초경량 재료인 글래스 버블을 적용해 무게를 줄인 것이 특징이다. 실러는 폴리비닐클로라이드(PVC) 수지에 각종 첨가제를 혼합해 만든다. 기존에는 탄산칼슘을 충전재로 사용했는데, 일부를 글래스 버블로 바꿔 무게를 줄인 것이다. 글래스 버블은 안이 비어 있어 가벼우면서도 크기가 매우 작은 미소구체(Microsphere)로, 경량 효과가 뛰어나 항공기나 건축물의 단열 충진재로 쓰인다.
글래스 버블과 폴리비닐클로라이드 수지를 혼합해 만든 초저비중 실러는 기존 실러 대비 37.5% 가벼우면서도 실러에 요구되는 물성들을 모두 만족한다. 덕분에 차량 1대당 약 3kg의 무게를 줄이는 효과가 있다. 쉽게 지나칠 수 있는 접착제에서도 복합소재를 이용해 경량화를 진행한 것이다. 이 밖에도 현대차·기아는 알루미늄, 합성수지, 열가소성 복합재료 등 다양한 소재를 이용해 차체의 무게를 줄이고 있다.
자동차 헤드램프는 주행 안전에 많은 영향을 미치는 부품이다. 빛의 밝기나 직진성을 높인 새로운 기술이 끊임없이 개발되는 이유다. 어떤 상황에서도 운전자가 시야를 확보하기 위해 램프가 깨끗하게 유지되는 것도 중요하다.
현대차·기아는 헤드램프 내부를 투명하게 유지하기 위해 복합소재를 활용하고 있다. 기존 헤드램프는 시간이 지날수록 불투명하게 변하는 특성이 있었다. 헤드램프 내부 온도가 200℃ 이상 상승하면서 플라스틱에서 발생한 가스가 램프를 착색시켰기 때문이다. 현대차·기아는 이 문제를 해결하기 위해 플라스틱 소재의 비중을 줄이고 유리 섬유와 고분자 첨가제를 더한 복합소재를 적용해 내열성을 확보했다. 이를 통해 가벼우면서도 투명함이 유지되는 램프를 개발할 수 있었다.
현대차 ST1의 루프 스포일러 제작에는 무도장 복합소재 성형기술이 적용됐다. 해당 기술은 소재 간 화학적 결합을 통해 외판과 내판의 물리적 접착 없이 제품을 만든다. 과정은 다음과 같다. 표현하고자 하는 색상의 플라스틱 원소재를 적층해 만든 컬러 시트에 열을 가해 연성을 높이고 금형에 올려 모양을 만든다. 이어 내측에 폴리우레탄과 유리 섬유를 도포하고 압축 성형을 통해 제품을 완성한다.
무도장 복합소재 성형기술을 적용한 ST1의 루프 스포일러는 기존의 루프 스포일러 대비 25% 가볍고, 외관 품질도 80% 뛰어나다. 기존의 루프 스포일러는 유리섬유, 탄소섬유, 아라미드섬유 등을 직접 쌓아 수지에 함침하고 후처리 과정을 거쳐 만들었다. 하지만 ST1의 루프 스포일러는 컬러시트, 폴리우레탄, 유리 섬유 등을 사용해 소재 밀도를 낮춘 덕에 가벼울뿐더러 소재 자체에서 색상을 구현하기에 도장을 하지 않아도 일관된 색상을 구현할 수 있다. 심지어 외부 충격에 의한 표면 긁힘이나 마모에도 색상을 유지할 수 있다.
탄소복합소재는 탄소를 모재로 강화재를 조합하여 만든 소재를 뜻한다. 모재로 탄소섬유, 강화재로 수지를 결합한 탄소섬유강화플라스틱이 대표적인 예다. 기존 자동차 산업에서 탄소섬유강화플라스틱 등의 탄소복합소재는 주로 레이싱카에 쓰였다. 가벼우면서도 견고하기 때문이다. 하지만 모빌리티 산업 전체로 시선을 넓히면 탄소복합소재의 쓰임새가 더욱 많아진다.
우선 현대차그룹은 탄소섬유강화플라스틱을 고성능 차량의 부품에 활용하고 있다. 대표적으로 아반떼 N, 아이오닉5 N 차량의 스포일러, 사이드 미러, 머플러 등에 탄소섬유강화플라스틱을 사용해 차체를 경량화하고 공력계수를 개선했다.
또한, 현대자동차그룹 로보틱스랩이 개발한 웨어러블 로봇 ‘엑스블 숄더(X-ble Shoulder)’에도 탄소섬유강화플라스틱이 적용됐다. 엑스블 숄더는 작업자의 상완(어깨) 근육을 보조하는 웨어러블 로봇이다. 작업 시간 동안 계속 착용하는 만큼 신체에 부담을 주지 않는 수준으로 무게를 줄이면서도 강성은 확보하기 위해 탄소섬유강화플라스틱을 적용했다.
엑스블 숄더는 무동력 토크 생성 구조로, 스프링의 탄성 에너지를 회전력 형태로 전달해 착용자의 상완 근력을 보조하는 ‘근력 보상 모듈’을 이용한다. 로보틱스랩은 해당 모듈의 내부 부품을 탄소섬유강화플라스틱과 유리섬유로 제작해 알루미늄 소재 대비 3.3배의 강성을 확보함과 동시에 중량은 40% 경감시켰다.
현대차 넥쏘와 같은 수소연료전지차에도 탄소복합소재가 사용된다. 고밀도 폴리머 라이너에 탄소섬유강화플라스틱 등 복합소재를 입혀 제작한 수소연료탱크가 대표적이다. 수소연료탱크의 내부 압력은 700바(bar)로 상당히 높다. 그만큼 안전한 저장을 위해 강도와 탄성이 우수한 복합소재를 사용한 것이다.
탄소복합소재 시장은 빠르게 성장하고 있다. 글로벌 시장조사 전문기관인 ‘마켓 앤 마켓(Markets and Markets)’이 2023년 발표한 보고서에서 탄소복합소재 시장 규모가 332억 달러 규모이며, 연평균 12.7% 성장해 2028년에는 603억 달러에 도달할 것으로 전망했다.
또한, 다른 시장조사 전문기관인 ‘리서치 앤 마켓(Research And Markets)’은 2025년 발표한 보고서를 통해 자동차, 풍력 에너지, 건설 분야에서 탄소복합소재의 사용이 증가하고 있다고 밝혔다. 급성장하는 전기차 산업이 경량 소재에 대한 수요를 주도하고 있으며 탄소복합소재가 금속의 대안이 되고 있다는 설명이다.
현재 탄소복합소재의 선두주자는 일본의 도레이(Toray)다. 도레이는 탄소섬유와 탄소복합소재 모두를 다룬다. 항공기 제조사인 보잉도 도레이의 탄소섬유를 사용할 정도다. 현대자동차그룹은 지난 2024년 4월 도레이와 미래 모빌리티 사업에 혁신 신소재를 적용하기 위한 전략적 협력 계약을 맺었다. 탄소섬유강화플라스틱 등을 공동 개발해 모빌리티의 성능과 안전성을 향상하고, 신소재를 적극적으로 적용해 모빌리티 산업의 혁신을 주도하기 위해서다.
또한, 현대자동차그룹은 올해 2월 코오롱그룹과 ‘전략적 미래 모빌리티 소재 사업 파트너십’을 체결했다. 자동차, 항공기 등에 쓰이는 소재를 개발 및 생산하는 코오롱스페이스웍스에 투자하고, 모빌리티 소재 경쟁력 강화를 위한 다양한 협력을 진행하겠다는 방침이다. 구체적으로는 수소저장용기 소재와 배터리 커버 성능 개선을 위한 공동 연구·개발을 진행하고, 유럽연합(EU)의 차량순환성 및 폐차관리규정(ELV) 등의 글로벌 환경규제에 대응하겠다는 계획이다.
현대자동차그룹은 친환경 미래 모빌리티의 기술 혁신을 위해 복합소재를 포함한 다양한 분야에 연구·개발을 진행하고 있다. 미래의 우리는 AAM, PBV, 로보틱스, 라스트마일 모빌리티 등 새로운 모빌리티를 통해 끊김 없는(Seamless) 이동의 자유로움을 누릴 것이다. 복합소재는 이와 같은 미래를 뒷받침하는 요소 중 하나이자, 미래 모빌리티의 완성도 향상과 혁신을 위한 열쇠 중 하나이기도 하다. 복합소재를 향한 현대자동차그룹의 새로운 시도에 우리가 주목해야 하는 이유다.