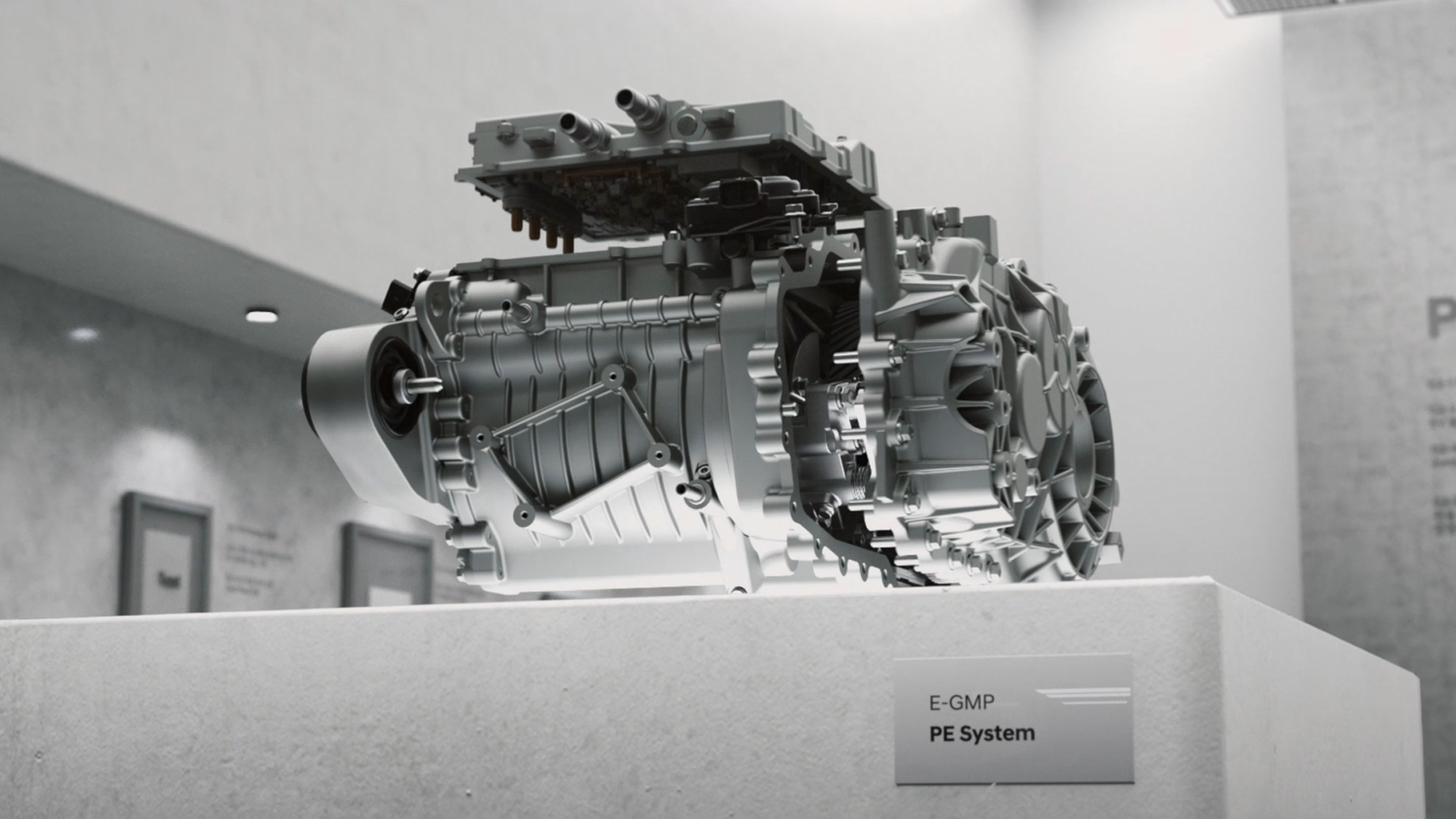
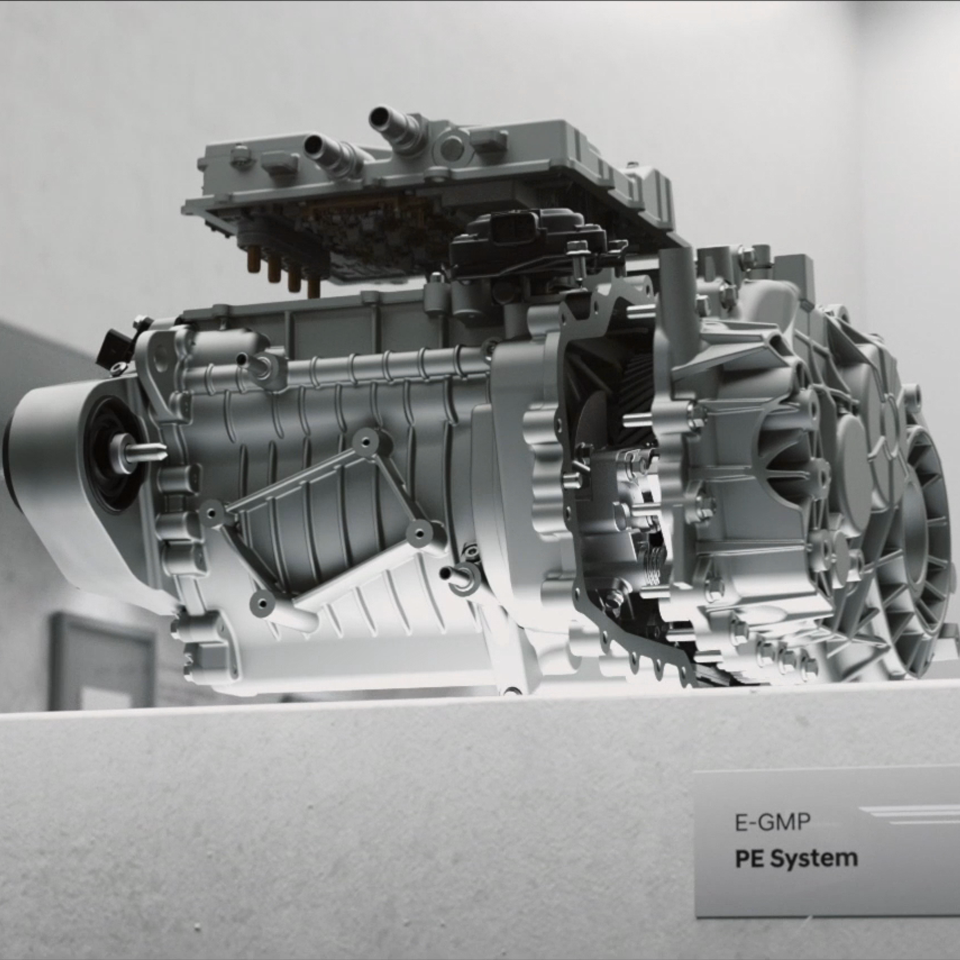
2022.03.02 현대자동차그룹
전기차 부품의 핵심 기술 PE(Power Electric)시스템으로부터 시작된 전기자동차의 시대
자동차의 시작은 언제일까? 흔히 1886년 최초의 내연기관 자동차가 등장하면서 자동차가 시작되었다고 말한다. 18세기에도 증기기관을 이용한 자동차가 있었지만 엔진의 유무로 판단하기 때문이다. 내연기관의 발명이 현대적인 자동차의 시작이라고 보는 것이다. 그렇다면 전기차의 시작은 어떻게 구분할 수 있을까? 전기차의 핵심이라고 볼 수 있는 PE(Power Electric)시스템, 즉 파워 일렉트릭 시스템을 통해 알 수 있다.
PE시스템이란 무엇일까? 기존 자동차에서 엔진의 역할을 하는 부품이다. 여기에는 모터, 인버터, 감속기가 들어간다. 2021년 출시한 현대자동차 아이오닉 5나 기아 EV6를 통해 일체형 PE시스템이라는 말을 들어본 적이 있을 것이다. 바로 모터와 인버터, 감속기를 통합하여 만들었다는 뜻이다.
배터리를 제외하면 전기차가 달리는데 가장 필수적인 부품이다. 엔진에서는 간접분사, 직접분사 혹은 4기통 6기통으로 구분하지만 전기차는 구분이 어렵고 자세히 구분해서 설명하지 않는다. 엔진과 PE시스템은 그 특징도 100년이 넘는 시간 동안 발전한 방향도 다르다. 전기차의 PE시스템은 짧은 시간에도 많은 변화가 일어났다.
불과 6년 전에 사용하던 모터와 인버터가 분리되고 주황색 3상 케이블로 연결했던 형태의 1세대 PE시스템은 2세대에서 모터와 인버터를 일체형으로 구성하면서 케이블과 커넥터를 없앴다. 최근 3세대 PE시스템은 모터와 인버터는 물론 감속기까지 합쳤다.
자동차로 세대를 구분한다면 2016년 정도까지 출시했던 쏘울 EV, 아이오닉 일렉트릭이 1세대이고 코나 일렉트릭, 니로 EV, 포터 일렉트릭이나 봉고 EV에 들어간 2017년에서 2019년까지 사용한 PE시스템이 2세대 정도로 구분할 수 있다. 2020년 이후 가장 최근 전기차에 적용한 PE시스템이 3세대라고 볼 수 있다. 이는 현대자동차그룹 E-GMP에 적용한 PE시스템이다. 이러한 변화를 거치면서 PE시스템은 발전을 더해가고 있다.
PE시스템의 발전을 통해 외부가 단순하게 변화한 것은 물론 효율에서도 변화가 이루어졌다. 2세대는 효율이 약 90%에서 92%로 개선되고 3세대는 약 94%까지 발전했다. 이는 모터의 최고 효율이 아니라 모터인버터 효율의 곱으로써 연비모드 운전점에서의 평균 효율을 의미한다.
불과 5~6년 사이에 출력밀도도 1.3kW/kg에서 지금은 3.0kW/kg으로 발전했다. 언뜻 1세대나 3세대나 그냥 외부가 조금 더 심플해진 것 외에는 기술적으로 어떻게 바뀌었는지 잘 구분되지 않을 수 있다. 하지만 3세대 PE시스템은 800V 고전압으로 충전 시간을 기존의 35분에서 18분으로 단축한 것이 특징이다. 기존의 전기차는 대부분 400V 시스템이기 때문에 별도의 승압기구 없이도 400V나 800V 충전기를 모두 사용할 수 있도록 만들어졌다.
또한 1세대가 출력 80kW, 최대속도 11,000rpm을 냈다면 3세대 PE시스템은 구동 모터를 기준으로 출력 160kW, 최대속도 19,000rpm의 성능을 낸다. 기아 EV6 GT 버전에 탑재될 모터는 출력 270kW, 최대속도 21,000rpm을 구현했다.
모양에서도 차이가 있다. 크기가 작아지며 높이가 기존 대비 30mm나 낮아졌다. 전기차에서 PE시스템의 높이를 낮추면 그만큼 실내 공간이나 트렁크의 크기를 더 확보할 수 있다. 또한 전륜은 물론 후륜에 넣기 적합하다. 작아진 만큼 냉각 성능도 중요한데 오일을 사용해 직접 냉각하는 방식을 사용해서 효율을 개선했다. 3세대 PE시스템은 전륜과 후륜에 각각 모터를 배치해 4륜구동을 적용하는 타입으로 개발되었다. 일체형이기 때문에 모터 위에 인버터가 위치하며 트렁크 공간을 차지하는 구조가 된다.
결국 모터와 인버터의 하우징을 일체화 하면서 인버터 높이를 기존 대비 30mm 가까이 낮추어 넉넉한 트렁크와 모터 인버터 일체형 PE시스템을 동시에 완성했다. PE시스템은 앞으로 얼마간 영구자석형 모터라는 큰 틀은 유지하면서 효율을 개선하고 원가를 절감하는 방향으로 발전할 것이다.
현재 가장 에너지가 높은 자석인 희토류 영구자석을 대체하는 재료가 등장하거나 더 좋은 성능의 철심코어, 저항이 낮은 구리 코일과 같은 재료 기술이 발전하면서 PE시스템 역시 함께 개선될 것이다. 1세대에서 부피를 줄이고 성능을 개선해 3세대 PE시스템을 개발한 것처럼 재료에서 시작해 구조 설계의 개발을 이뤄내며 차근차근 발전해 나갈 것이다.